How to re-string a guitar
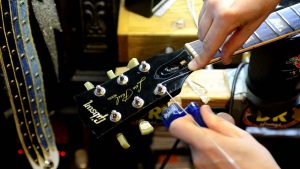
It might sounds ridiculous to some, but it’s true: some beginner guitarists often don’t know how to replace strings. This quick guest blog will help them out. Guitar’s strings are usually durable enough to withstand months after they need to be changed, but don’t think that a popped string is the only reason why you […]